
PLASTIC MODULAR
Simple cleaning, maintenance, and repair with long life for virtually every type of conveyor.
Plastic Modular Belts are assembled in a bricklay pattern, allowing for endless lengths and widths. Material options include polypropylene, polyethylene, acetal and nylon. Modular belts can vary in hardness, temperature and chemical resistance, strength, density and coefficient of friction depending on the application.
They are positively driven by sprockets engaged with the underside of the belt. They are low noise, long lasting and have strong sanitary properties.
Most plastic modular belts are FDA compliant.
Ease of maintenance and efficiency improving advantages set plastic modular apart from other types of belt. Repair is simple as damaged portions can easily be extracted and replaced with no need to remove the entire belt.
Plastic modular belts have been proven to be both rot resistant and durable.
Available accessories include flights, sideguards, wearstrips, retainer rings, and finger transfer plates. Blankenship Belting offers both split and single-piece sprockets (plastic or metal).

ADVANTAGES INCLUDE
-
Longer belt life with less belt wear
-
Simplified cleaning and maintenance
-
Reduced risk of product loss or contamination
-
Variety of materials and configurations
-
Enhanced worker safety
-
Fewer Pulleys due to low tension
-
Zero need for lubrication or tensioning
-
Positive Drive

TURN BELTS
Spiral conveyors which use vertical height to save floor space can benefit from the advantages of plastic modular belting. Plastic modular turn belts can make tight turn radiuses and its temperature tolerance makes it a great choice for cooling applications.

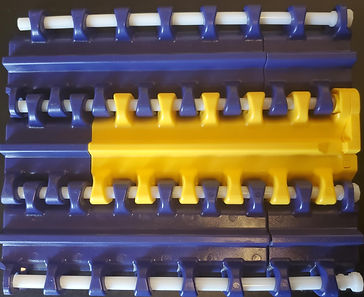